Chemical reactors are key pieces of equipment used in the pharmaceutical industry to produce drugs and other pharmaceutical products. A chemical reactor is a vessel or container in which chemical reactions take place. In the pharmaceutical industry, chemical reactors are used to carry out chemical synthesis, purification, and other chemical processes that are essential for the production of drugs.
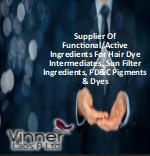
Chemical reactors in pharmaceuticals come in different sizes and designs, depending on the specific process and the desired output. Some common types of reactors used in pharmaceuticals include batch reactors, continuous flow reactors, and fixed bed reactors.
In batch reactors, a specific amount of reactants is added to the vessel, and the reaction is allowed to proceed until the desired product is obtained. Continuous flow reactors, on the other hand, operate continuously, with reactants being continuously fed into the reactor and products being continuously removed. Fixed bed reactors involve the use of a solid catalyst bed that facilitates the reaction between the reactants.
Chemical reactors are critical to the pharmaceutical industry because they enable the production of pure and high-quality drugs. They also play a key role in the development of new drugs and the optimization of drug production processes.
Maintaining chemical reactors is critical in ensuring quality end products in the pharmaceutical industry. Proper maintenance of reactors helps prevent equipment failure, contamination, and product defects. Here are some key maintenance activities that are important to consider for chemical reactors in the pharma industry:
Regular inspections: Regular inspections of chemical reactors should be carried out to identify any signs of wear, corrosion, or other damage that could lead to equipment failure. This can help prevent downtime and reduce the risk of product defects.
Cleaning and sanitization: Chemical reactors must be cleaned and sanitized regularly to prevent the buildup of contaminants and maintain product quality. Proper cleaning and sanitization procedures should be developed and followed to ensure that the reactors are free from bacteria, viruses, and other harmful substances.
Calibration and testing: Regular calibration and testing of sensors and other instruments are critical to ensure that chemical reactions are occurring as intended. This can help identify any deviations from the desired reaction conditions and allow for corrective action to be taken.
Replacement of worn or damaged parts: Worn or damaged parts in chemical reactors should be replaced promptly to prevent equipment failure and ensure product quality.
Training of operators: Proper training of operators is critical to ensure that chemical reactors are operated safely and effectively. Operators should be trained in the proper use of equipment, safety procedures, and maintenance protocols.
By following these maintenance activities, pharmaceutical companies can help ensure that their chemical reactors are operating efficiently and producing high-quality end products.